1.Karolo ea karolo e 'ngoe le e 'ngoe ea setlamo sa taemane sa blade matrix ke efe?
Karolo ea koporo: Li-alloys tse thehiloeng ka koporo le tsa koporo ke litšepe tse sebelisoang haholo lisebelisoa tsa taemane tse tlamang ka tšepe, 'me phofo ea koporo ea electrolytic ke eona e sebelisoang haholo.Li-alloys tsa koporo le tsa koporo li sebelisoa haholo hobane li-binders tse thehiloeng ho koporo li na le thepa e khotsofatsang: mocheso o tlase oa sintering, sebopeho se setle le sinterability, le miscibility le likarolo tse ling.Leha koporo e sa kolobise litaemane, likarolo tse ling le lialloys tsa koporo li ka ntlafatsa haholo ho koloba ha tsona ho litaemane.E 'ngoe ea lintho tse kang Cr, Ti, W, V, Fe tse etsang koporo le li-carbides li ka sebelisoa ho etsa li-alloys tsa koporo, tse ka fokotsang haholo angle ea ho koloba ea li-alloys tsa koporo holim'a litaemane.Ho qhibiliha ha koporo ka tšepe ha ho phahameng.Haeba ho na le koporo e feteletseng ka tšepe, e fokotsa haholo ts'ebetso ea mocheso mme e baka ho phatloha ha thepa.Koporo e ka etsa litharollo tse fapaneng tse tiileng ka nickel, cobalt, manganese, tin le zinki, e matlafatsang tšepe ea matrix.
Mosebetsi oa thini: Tin ke ntho e fokotsang tsitsipano ea holim'a li-alloys tsa metsi 'me e na le phello ea ho fokotsa angle ea ho koloba ea li-alloys tsa metsi holim'a litaemane.Ke ntho e ntlafatsang ho kolobisoa ha litšepe tse tlanngoeng ka litaemane, ho fokotsa ntlha ea ho qhibiliha ha li-alloys, le ho ntlafatsa sebopeho sa ho hatella.Kahoo Sn e sebelisoa haholo ho li-adhesive, empa tšebeliso ea eona e lekanyelitsoe ka lebaka la coefficient ea eona e kholo ea ho atolosa.
Karolo ea zinki: Lithulusing tsa daemane, Zn le Sn li na le lintho tse ngata tse tšoanang, tse kang ntlha e tlaase ea ho qhibiliha le ho holofala hantle, ha Zn e se e ntle ho fetola mongobo oa daemane joaloka Sn.Khatello ea mouoane ea tšepe ea Zn e phahame haholo 'me e bonolo ho khase, kahoo ke habohlokoa ho ela hloko palo ea Zn e sebelisoang li-binders tsa lisebelisoa tsa daemane.
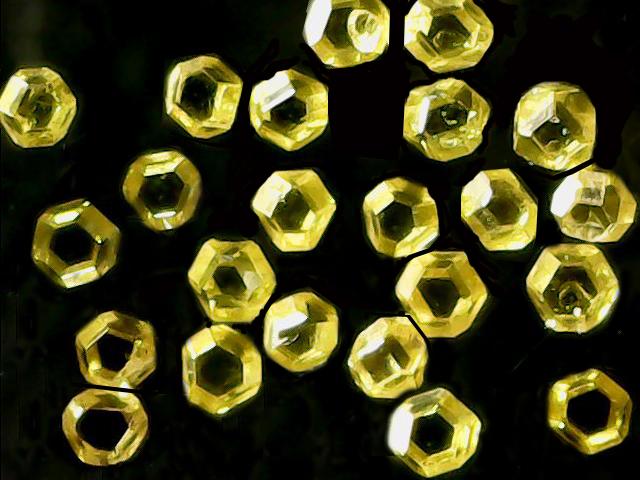
Karolo ea aluminium: Metal aluminium ke tšepe e khanyang e khanyang le deoxidizer e ntle.Ho 800 ℃, angle ea ho koloba ea Al holim'a taemane ke 75 °, 'me ho 1000 ℃, angle ea ho koloba ke 10 °.Ho eketsa phofo ea aluminium ho se tlamang lisebelisoa tsa daemane ho ka etsa karolo ea carbide Ti Å AlC le motsoako oa intermetallic TiAl ka har'a motsoako oa matrix.
Karolo ea tšepe: Tšepe e na le karolo e 'meli ho se tlamang, e' ngoe ke ho etsa li-carburized carbides tse nang le litaemane, 'me e' ngoe ke ho kopanya le likarolo tse ling ho matlafatsa matrix.Ho koloba ha tšepe le daemane ho molemo ho feta koporo le aluminium, 'me mosebetsi oa ho khomarela pakeng tsa tšepe le daemane o phahame ho feta oa cobalt.Ha palo e loketseng ea khabone e qhibilihisoa ka li-alloys tsa Fe, ho tla ba molemo bakeng sa tlamahano ea bona le litaemane.Ho hlophisoa ha litaemane ka mokhoa o itekanetseng ka li-alloys tsa Fe ho ka eketsa matla a tlamahano pakeng tsa tlamo le daemane.Sebaka sa ho robeha ha se boreleli ebile ha se letho, empa se koahetsoe ke lera la alloy, e leng pontšo ea matla a matla a ho kopanya.
Karolo ea cobalt: Co le Fe ke karolo ea likarolo tsa sehlopha sa phetoho, 'me litšobotsi tse ngata li tšoana.Co e ka theha carbide Co ₂ C ka daemane tlasa maemo a ikhethileng, ha e ntse e jala filimi e tšesaane haholo ea cobalt holim'a daemane.Ka tsela ena, Co e ka fokotsa tsitsipano ea ka hare ea sefahleho pakeng tsa Co le daemane, 'me e na le mosebetsi oa bohlokoa oa ho khomarela daemane karolong ea mokelikeli, e leng se etsang hore e be thepa e ntle ea ho kopanya.
Karolo ea nickel: Setlamong sa lisebelisoa tsa daemane, Ni ke ntho ea bohlokoa haholo.Ho li-alloys tsa Cu, ho eketsoa ha Ni ho ka qhibiliha ka ho sa feleng ka Cu, ho matlafatsa motsoako oa matrix, ho hatella tahlehelo ea tšepe e tlase, le ho eketsa boima le ho hanyetsa.Ho kenyelletsa li-alloys tsa Ni le Cu ho Fe ho ka theola mocheso oa sintering le ho fokotsa ho bola ha litšepe tse tlanngoeng ka litaemane.Ho khetha motsoako o nepahetseng oa Fe le Ni ho ka ntlafatsa haholo matla a ho tšoara li-binders tsa Fe holim'a litaemane.
Karolo ea manganese: Litlamong tsa tšepe, manganese e na le phello e ts'oanang le tšepe, empa e na le matla a ho phunyeletsa le matla a ho ntša oxygenation, 'me e atisa ho ba le oxidation.Palo ea tlatsetso ea Mn ka kakaretso ha e phahame, mme ho nahanoa haholo ke ho sebelisa Mn bakeng sa deoxidation nakong ea sintering alloying.Mn ea setseng a ka kenya letsoho ho kopanya le ho matlafatsa matrix.
Karolo ea chromium: Metal chromium ke ntho e matla e etsang carbide hape ke ntho e sebelisoang haholo.Ka har'a taemane groove saw blade matrix, ho na le chromium e lekaneng ho ba le phello ea ho fokotsa molumo, e amanang le matla a ts'ebetso ea Cr.Ho eketsa palo e nyane ea Cr ho Cu based matrix ho ka fokotsa angle ea ho koloba ea motsoako oa koporo ho ea ho daemane le ho ntlafatsa matla a ho kopanya a alloy ea koporo ho daemane.
Karolo ea titanium: Titanium ke ntho e matla ea ho etsa carbide e bonolo ho oxidize le eo ho leng thata ho e fokotsa.Boteng ba oksijene, Ti ka mokhoa o ikhethileng e hlahisa TiO2 sebakeng sa TiC.Titanium tšepe ke thepa e ntle ea sebopeho e nang le matla a matla, phokotso ea matla a fokolang mochesong o phahameng, ho hanyetsa mocheso, ho hanyetsa kutu, le ntlha e phahameng ea ho qhibiliha.Lipatlisiso li bontšitse hore ho eketsa tekanyo e loketseng ea titanium ho matrix a lehare la taemane ho molemo bakeng sa ho ntlafatsa bophelo ba tšebeletso ea lehare la sakha.
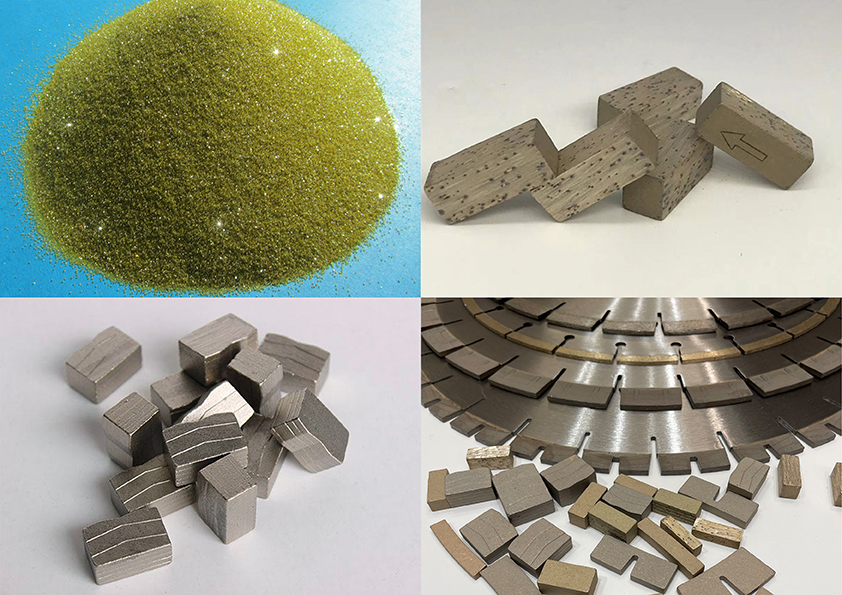
2.Ke hobane'ng ha 'mele oa lehare la sakha o lokela ho tšoana le lejoe le sehang?
Mekhoa e ka sehloohong ea ho petsoha ha majoe nakong ea ts'ebetso ea ho seha lehare ke ho pshatla le ho pshatla, hammoho le ho kuta le ho arola ha molumo o moholo, ho tlatselletsoa ke ho sila holimo.Taemane e nang le sebaka sa ho sebetsa se serrated se sebetsang joalo ka sesebelisoa sa ho itšeha.Sebaka sa eona sa ho itšeha ke sebaka sa extrusion, sebaka sa ho itšeha se ka pel'a moeli, 'me sebaka sa ho sila se ka morao.Tlas'a ho itšeha ka lebelo le phahameng, likaroloana tsa daemane li sebetsa ho ts'ehetso ea matrix.Nakong ea ts'ebetso ea ho seha lejoe, ka lehlakoreng le leng, daemane e na le graphitization, fragmentation, le detachment ka lebaka la mocheso o phahameng o hlahisoang ke khohlano;Ka lehlakoreng le leng, matrix e apesoa ke ho hohlana le khoholeho ea majoe le phofo ea majoe.Ka hona, taba ea ho ikamahanya le maemo pakeng tsa li-saw blades le majoe ha e le hantle ke taba ea sekhahla sa ho apara pakeng tsa daemane le matrix.Sebopeho sa sesebelisoa se sebetsang ka mokhoa o tloaelehileng ke hore tahlehelo ea daemane e tsamaisana le moaparo oa matrix, e boloka taemane e le maemong a tloaelehileng a ho itšeha, e se ho koaheloa pele ho nako kapa ho sila taemane e boreleli le e thellang, ho netefatsa hore phello ea eona ea ho sila e sebelisoa ka botlalo. nakong ea ts'ebetso, ho etsa hore litaemane tse ngata li be boemong bo robehileng le bo tsofetseng.Haeba matla le ts'usumetso ea ho hanyetsa ha daemane e khethiloeng e le tlaase haholo, e tla lebisa ketsahalong ea "ho kuta", 'me nako ea bophelo ea sesebelisoa e tla ba e tlaase' me passivation e tla ba e matla, esita le ho sakha ho ke ke ha sisinyeha;Haeba ho khethoa likaroloana tsa abrasive tse matla ka ho feteletseng, moeli oa ho itšeha oa likaroloana tsa abrasive o tla hlaha sebakeng se bataletseng, se hlahisang keketseho ea matla a ho itšeha le ho fokotseha ha ts'ebetso ea ts'ebetso.
(1) Ha lebelo la ho roala ha matrix le le leholo ho feta la daemane, le lebisa ho ho itšeha ho feteletseng ha daemane le ho arohana pele ho nako.Ho hanyetsa ho roala ha 'mele oa lehare la saw ho tlase haholo,' me bophelo ba lehare la sakha bo bokhutšoanyane.
(2) Ha lebelo la ho roala ha matrix le le ka tlase ho la daemane, daemane e ncha ha e pepesoe habonolo ka mor'a hore daemane e sehiloeng e koaloe, li-serrations ha li na moeli oa ho itšeha kapa moeli oa ho itšeha o tlase haholo, bokaholimo ba marang-rang. li-serrations li fetisitsoe, lebelo la ho itšeha le lieha, 'me ho bonolo ho etsa hore boto e sehiloeng e oe, e amang boleng ba ho sebetsa.
(3) Ha lebelo la ho roala ha matrix le lekana le lebelo la ho roala ha daemane, le bonahatsa ho lumellana ha matrix le lejoe le sehiloeng.
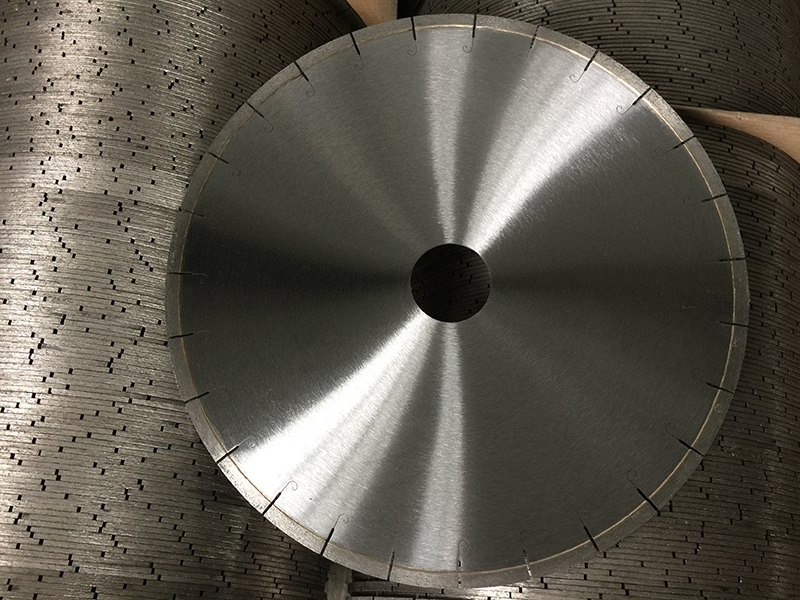
Nako ea poso: Aug-11-2023